TechEmerge – Our Search For Sustainable Refrigeration
Câm was one of 15 companies selected by IFC’s TechEmerge Program to pilot sustainable cooling technologies.
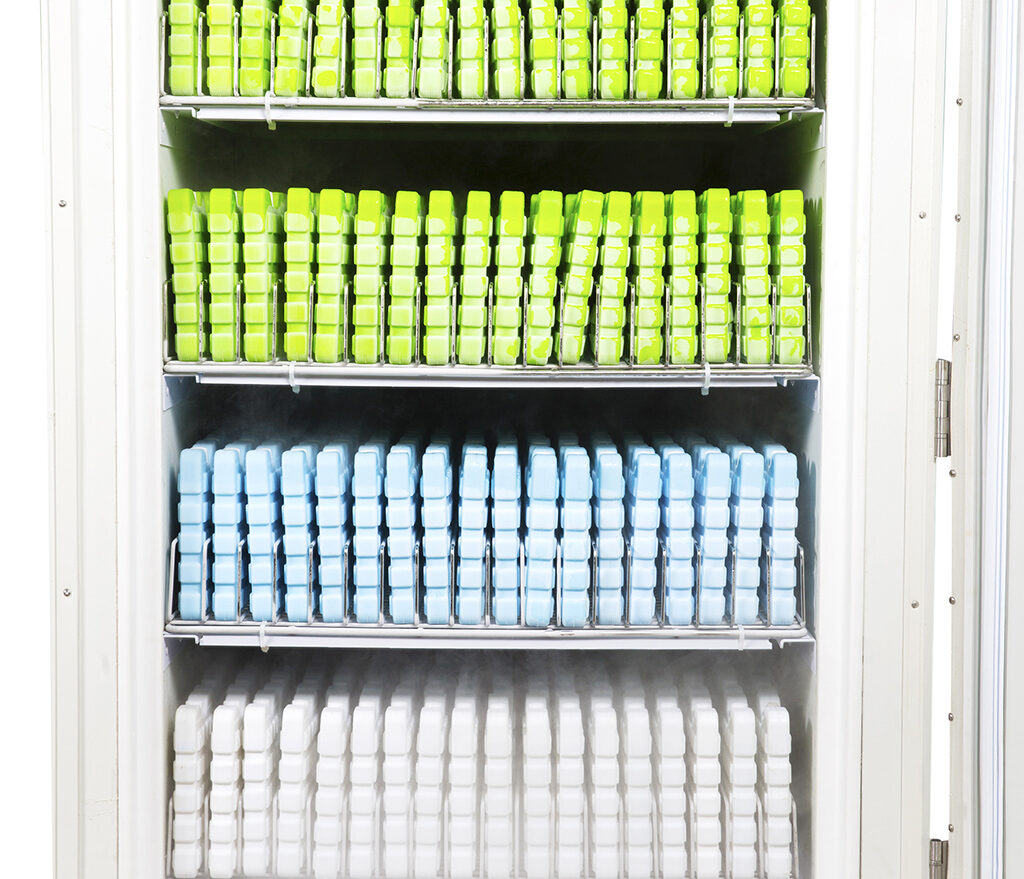
Câm was one of 15 companies selected by IFC’s TechEmerge Program to pilot sustainable cooling technologies.
When we launched Câm, we knew there would be challenges. With no suitable blueprint to follow and no other company producing fresh dairy at scale in Nigeria, we had to figure things out for ourselves and form relationships with equally innovative partners.
One such obstacle was refrigeration.
Our unpasteurised milk must be kept below 4°C in transit (bear in mind the average temperature outside is often +30°C). The distance between the pastoralist communities where our milk comes from and our dairy factory in Abuja involves hours of driving on poorly surfaced roads.
Since our dairy comes from real cows and isn’t heavily processed or heat treated like UHT and evaporated milk, our fresh dairy products must also be refrigerated.
Our options for refrigeration were limited
Before IFC’s TechEmerge Program (which was launched in Nigeria in collaboration with Kobo 360), the only option was to use what’s called a ‘standard vapour compression system’. When used in transportation, this refrigeration method is powered by a combination of CFC gases and a higher consumption of diesel/petrol from the vehicle.
Since the Nigerian dairy industry is in the early stages of growth, we’re striving to build a supply chain that reduces environmental impact wherever possible.
Our search led us to IFC’s TechEmerge Program.
IFC was looking for just 15 companies across the food and pharmaceutical industries to pilot a sustainable approach to refrigeration. Successful applicants would be matched with innovative companies worldwide to tackle some of the world’s most pressing challenges, especially in emerging markets.
There were a number of challenges we hoped to overcome through the program – from unreliable access to grid electricity (leading to the use of diesel generators) through to lack of real-time analytics into our cold chain operations. Our objective was to test sustainable refrigeration solutions in our vehicles and monitor the performance and efficiency of these solutions via GRICD Mote devices.
“The TechEmerge Program supported by IFC and Kobo360 was able to produce an excellent solution for Câm taking into account the developing phase of the company. Câm is at a much smaller scale while introducing real dairy products into the Nigerian market.”
– Spokesperson from Kobo 360*
After being accepted into the program, IFC matched us with an Indian-based cold chain logistics company, Tessol, who helped develop a passive refrigeration solution for Câm that can be scaled to support our growing volumes of milk.
The benefits of passive refrigeration
Instead of CFC gas, Tessol’s solution uses innovative materials called Phase Change Materials (PCM). These chemicals can store thermal energy and slowly release it over a required period of time enabling accurate temperature control during transportation of perishable goods.
The beauty of this technology is that it can be used for short trips around Lagos to long-distance trips between states. In addition, because we often travel on poorly maintained roads, the refrigeration units contain no moving parts, reducing maintenance from vibrations and impact. We’re now using Tessol’s solution on some of our fleet vehicles for the pilot stage. This means we’re already much less reliant on fossil fuels or harmful CFC gases to keep our milk cool. The PCM technology is also deployed in the form of refrigerated cartridges, which we are using in insulated boxes mounted on motorbikes. This is particularly useful for door-to-door deliveries in cities like Lagos, where motorbikes are better suited to navigating heavy traffic.
What IFC’s pilot means for Câm (and the rest of the industry)
We know refrigeration isn’t the most glamorous thing to talk about, but the implications are far-reaching.
There are several outcomes we’re hoping for from IFC’s TechEmerge Program before we decide whether to adopt passive cooling across our fleet. By the end of the pilot, we hope to reduce fuel consumption for refrigeration units (which lessens greenhouse gas emissions) and see an operational cost saving. In other words, it should cost us less to deliver a litre of milk, which could lead to a saving being passed on to customers.
We’re also working with a second partner on this project, GRICD. They are providing the temperature monitoring devices that give us real-time temperature readings, send email alerts when the temperature is out of range (which means we can fix problems quickly) and provide us with GPS location data so that we know where our products are at all times.
However, smart refrigeration solutions can ultimately benefit the entire industry, both in Nigeria’s emerging market and in the world’s most developed and fastest-growing dairy producing countries – from India and Brazil to the United States.
By sharing our knowledge and working in partnership with others, we can significantly reduce the environmental impact of the dairy industry and design future-proof infrastructure to continue producing accessible nutrition.